Access and insights:
your hub for Cyclic Materials
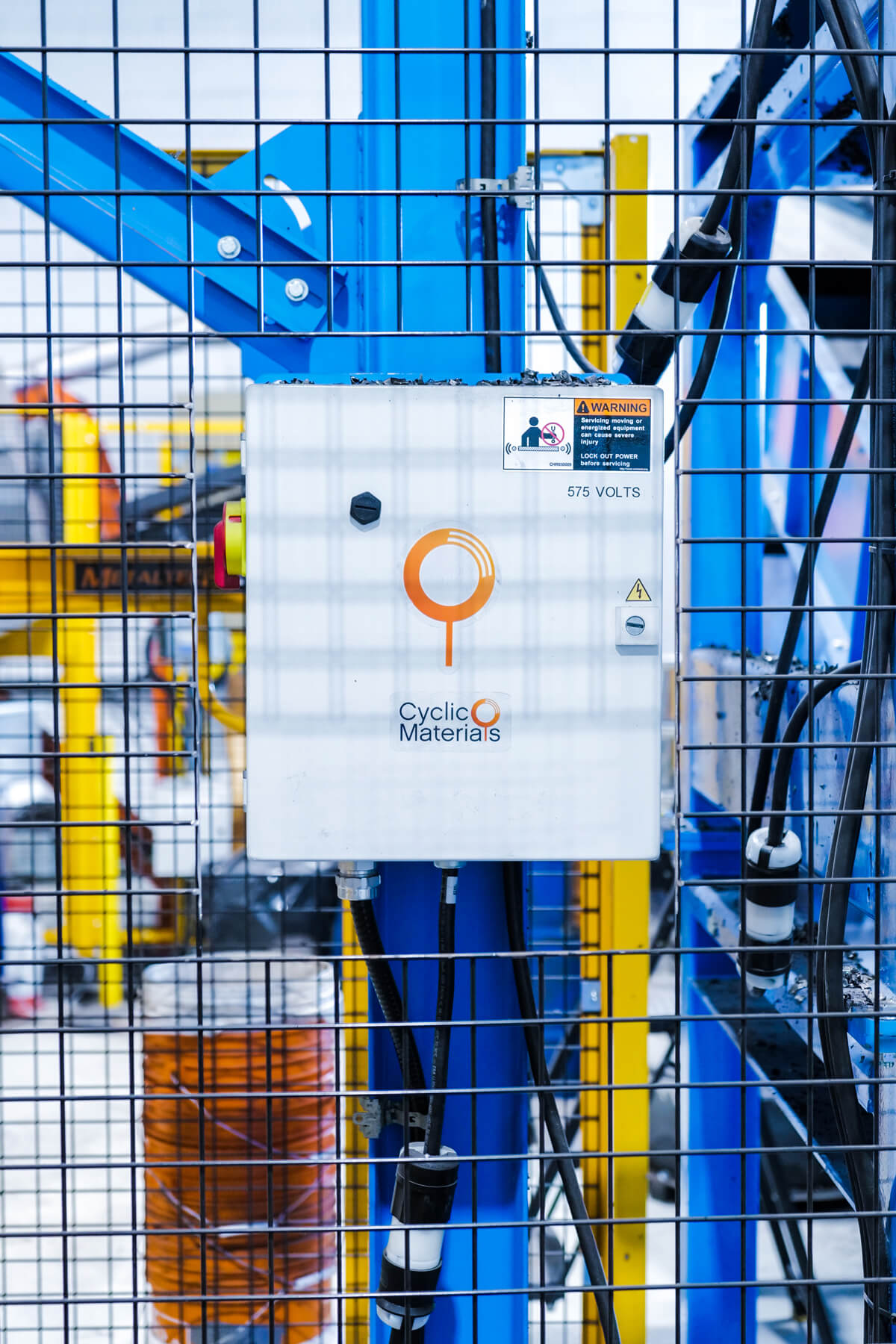
Asset library
Looking for official Cyclic Materials brand assets? Our Asset Library includes downloadable resources like our media kit, logos, and other essential materials to support your coverage and collaborations.
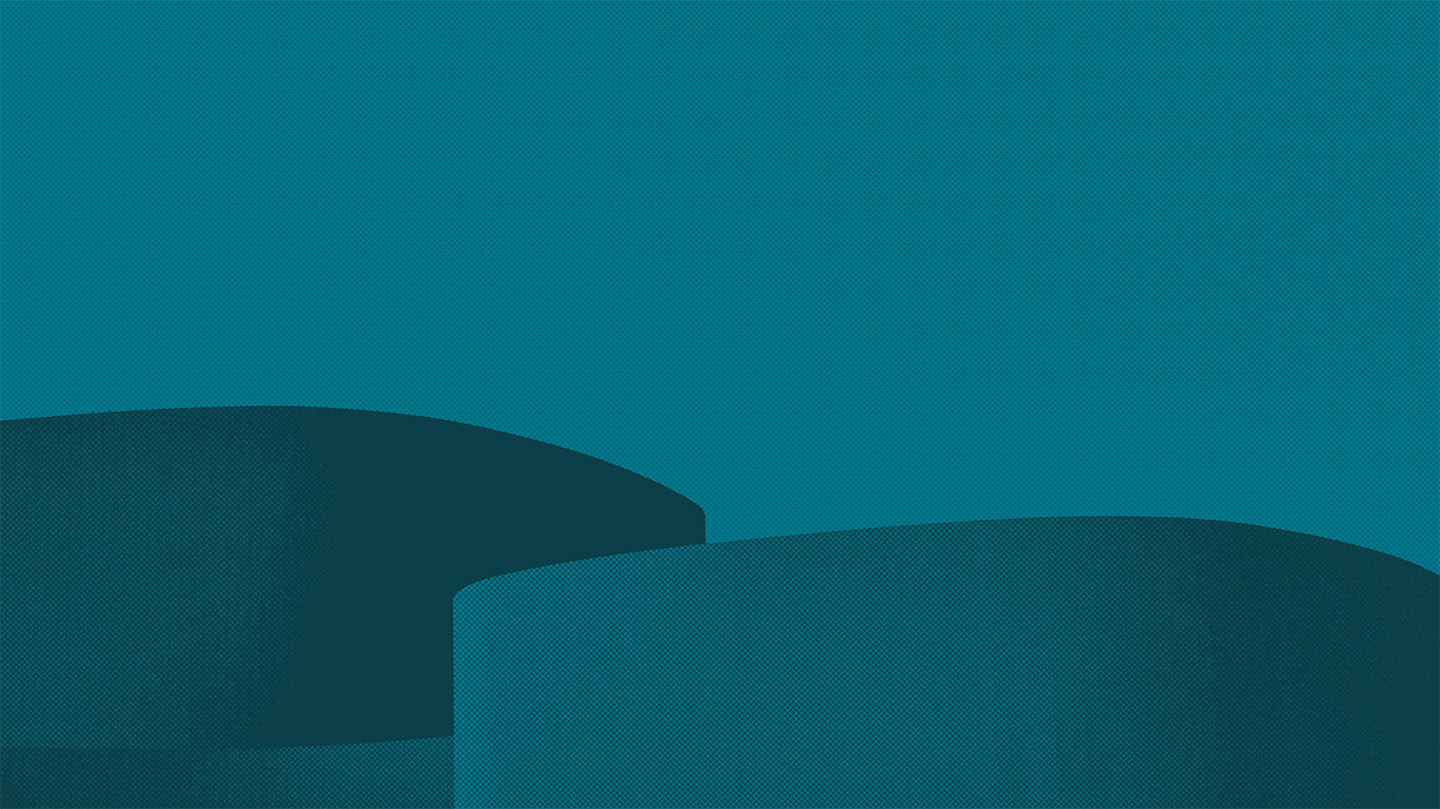
Recycle with us
Help keep critical materials in circulation
Reduce waste through our innovative recycling solutions.
Connect with us
Let’s build a sustainable future together
Explore opportunities to collaborate for lasting impact.