A New Milestone in Creating a Circular Supply of Critical Materials
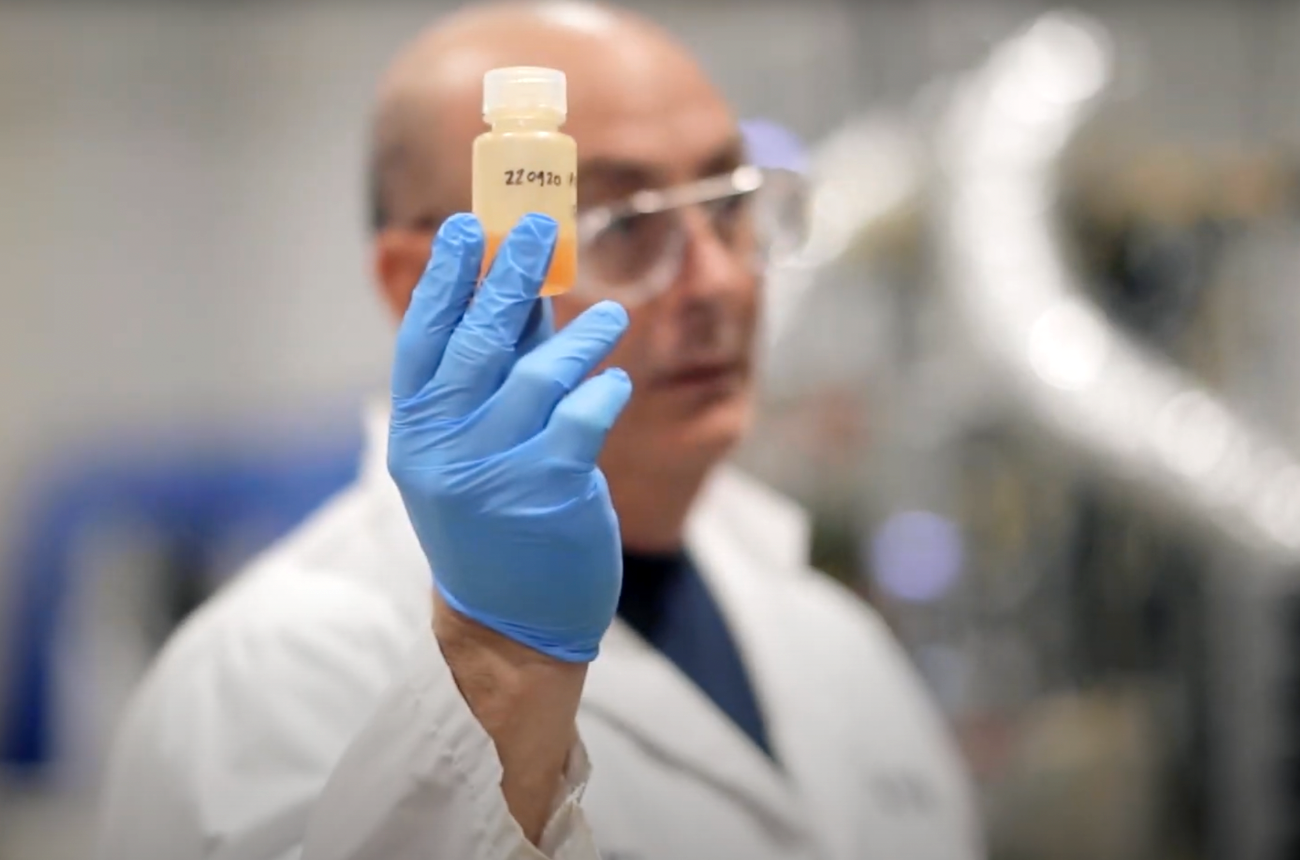
Cyclic Materials, a startup building a domestic supply chain for rare earths, has reached another milestone in the scale up of its groundbreaking technology.
Rare earths are metals used in electric vehicles, wind turbines, and many other high technology devices, and they are identified as critical to industrial and defense applications by countries around the world. Their applications are growing so rapidly that the mining of rare earth elements cannot keep up with demand, with shortages of almost one third of demand projected in the near future. These shortages risk derailing the ambitious plans of auto manufacturers and wind turbine companies.
Cyclic Materials is pleased to announce the completion of the initial production run at its magnet recycling pilot plant, focused on generating the engineering data required for its 2023 scale up plans and producing high quality magnet rare earth oxides. This achievement marks another successful milestone in the development of Cyclic Materials groundbreaking magnet recycling system which the company is initially using to build a North American supply chain for rare earth elements. Cyclic Materials aims to produce 600 tons of mixed rare earth oxides by 2026, increasing to 3,000 tons per year by 2030.
“We are helping the world transition to an environmentally responsible future by recovering rare earth elements from the difficult-to-recycle products of the modern world,” said Ahmad Ghahreman, CEO and co-founder of Cyclic Materials. "We are proud to contribute in such a foundational way to the electrification of mobility and to green energy. With continued support of industrial and government partners, we intend to continue the scale up of our technology at this blistering pace because every day of delay results in fewer EVs on the road and fewer wind turbines generating power.”
With the production of these larger samples from its pilot plant, Cyclic Materials is able to provide material to partners in the supply chain, including magnet and automobile manufacturers. With these materials in hand for validation, new partnerships are being created to reinforce a reliable supply of magnets to industry.
In addition to the supply chain advantages, Cyclic Materials’ recycled rare earths have a dramatically lower environmental impact when compared against the extraction and processing of these materials from a mine. Responsible land use is improved by avoiding the earth removal of mining, carbon dioxide is reduced because no mined earth needs to be processed, and water quality is protected with Cyclic Materials’ closed-loop process that consumes less than 2% of the water consumed when mining rare earths. With most rare earth mineral mining and processing currently being completed in China, Cyclic Materials’ recycling process will also help reduce carbon emissions associated with transportation of rare earth minerals.
By recycling devices at the end of life, Cyclic Materials recovers materials from local resources without the need to build a local mine, a process that takes as much as 10 years to approve. With a local supplier of rare earth elements, downstream partners in the supply chain can invest in new facilities with confidence that there will be a consistent and local supply of rare earth elements.
"Local industry can create magnets, which are critical components for electric vehicles and wind turbines, only if it has access to the required raw materials," says Cyclic Materials co-founder Patrick Nee. "We are working with multiple companies that plan to build processing and manufacturing facilities in North America, all of which require access to rare earths. Our materials are of higher purity than those produced at mines and will accelerate the development of these important industries."
The next steps for Cyclic Materials include building its first fully integrated and continuous commercial plant for mixed rare earth production. This plant is expected to produce cobalt and nickel, as well as other minor by-products such as boron-based materials. Cyclic Materials will also build a scaled-up high-capacity pilot plant for the processing of end-of-life products. These milestones are expected to be delivered in 2023.